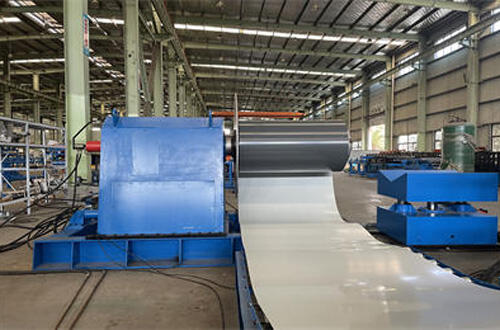
- Overview
- Inquiry
- Related Products
Product Details
1. Each uncoiler drives the sprocket through the hydraulic motor, and drives the main engine through the sprocket, so that the steel coil rotates with the main shaft.
2. To achieve the purpose of auto uncoiler, the base and frame of the uncoiler are all welded by rectangular tubes, which fully guarantees the rigidity of the machine.
3. Reel: four pieces of nesting (shoes), available in 508 and 610 sizes, when 508 steel coil is switched to 610 inner hole steel coil, four arc plates are added to the original uncoiler to automatically support Ttght and constant tension control.
4. Transmission system: forward and reverse to realize the rewinding and unwinding, the unwinding mandrel is driven by the motor and the reducer to realize the automatic opening of the steel coil, and it can also be used for the recovery of the plate that has not been processed; when the material is automatically opened, it can maintain same tempo as production.
5. The pressing deviceis to swing the pressing arm through the cylinder. When the cylinder rises, the pressing arm is loosened; when the cylinder is lowered, the pressing arm is pressed tightly. The adjustment of the coil center of the uncoiler is realized by the hydraulic cylinder, which is convenient to adjust and easy to operate; when the coil is automatically uncoiled, the pressing arm must loosen the steel coil, and when the machine stops, the pressing arm must press the steel coil.
6. Lifting trolley: The lifting trolley is driven by the motor to make the trolley walk along the guide rail, and the lifting device is driven by the hydraulic cylinder through the lifting platform for the connecting rod to complete the loading and unloading actions. The lifting platform and the walking platform adopt the mixed welding structure of rectangular tube and steel plate, and the appearance is beautiful.
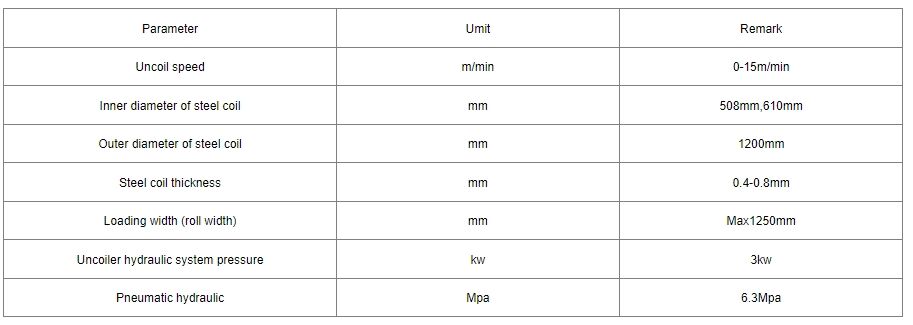
Company and Service Advantages:
2.The company has a professional The Adjuster team, 24 hours to provide uninterrupted after-sales service.
(1) Installation and debugging
Equipment arrived at the customer workshop, according to the flat layout of our equipment. We will arrange experienced technicians to install, debug and test-produce the equipment, and make the equipment reach the rated production capacity of the production line.
(2) Training
Our company provides technical training for our customers. The training includes the structure and maintenance of the equipment, the control and operation of the equipment, experienced technicians will guide and establish the training program. After training, the buyer's technical personnel can master the operation and maintenance of the equipment, can adjust the process and deal with different failures.
3.After-sales quality problems within 2 hours to answer, if the telephone video guidance can not be solved, domestic 24 hours to send engineers to the site to solve the problem.
4. Factory direct sales price concessions, 40,000 square meters factory, 20 years of Export Enterprises, CE certification, patents more than 100 items.
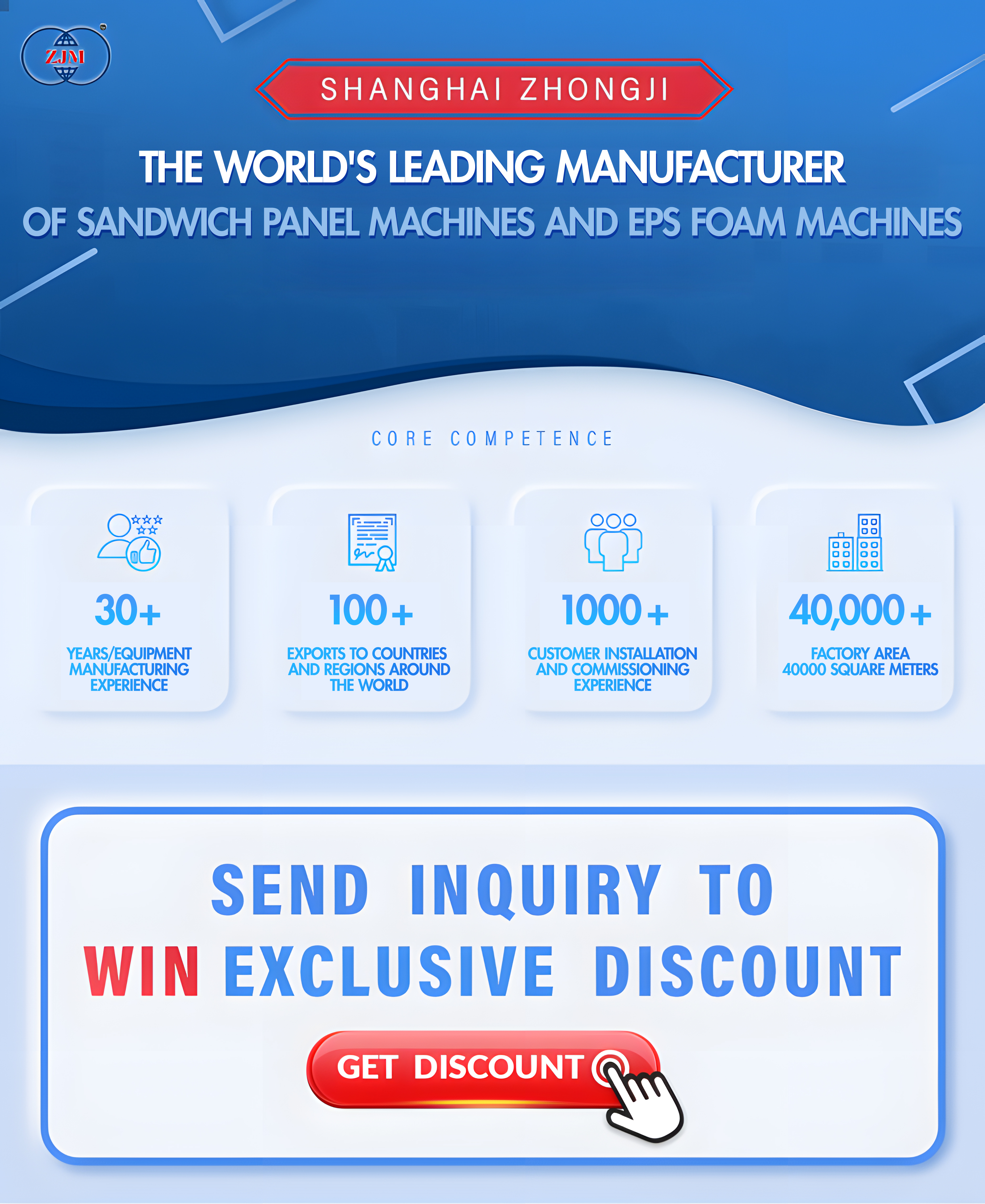
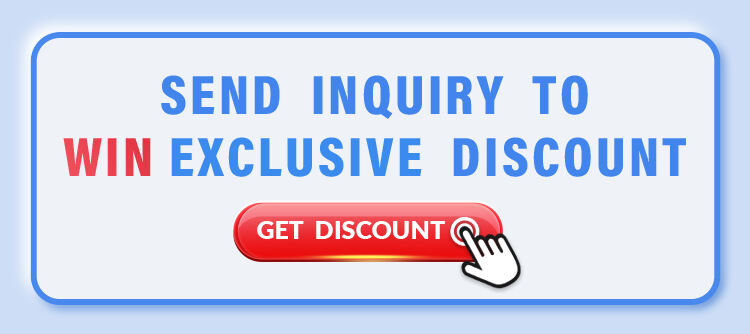
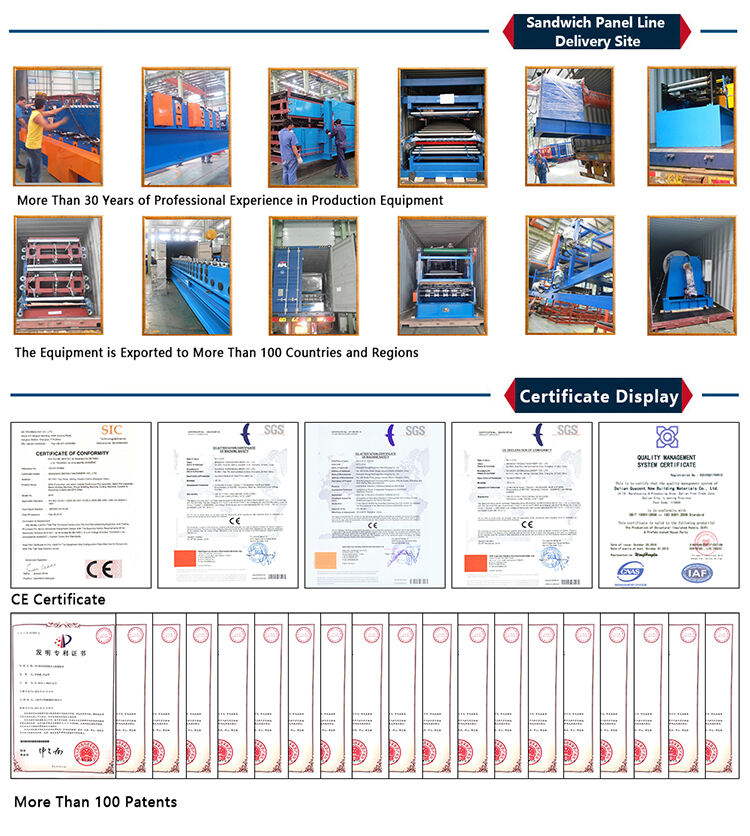
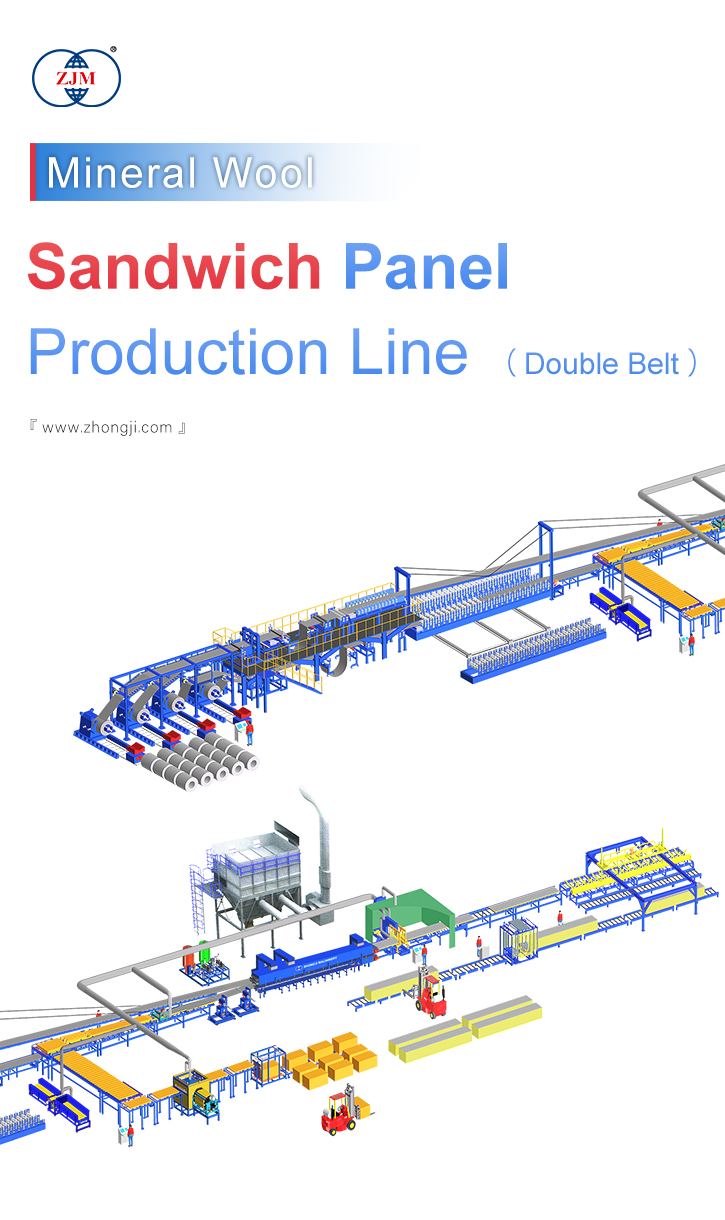
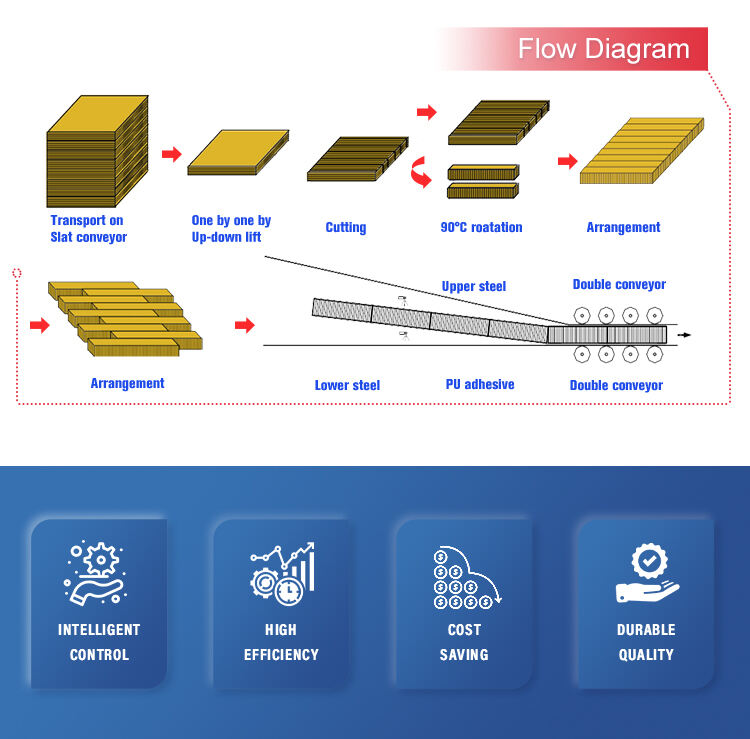
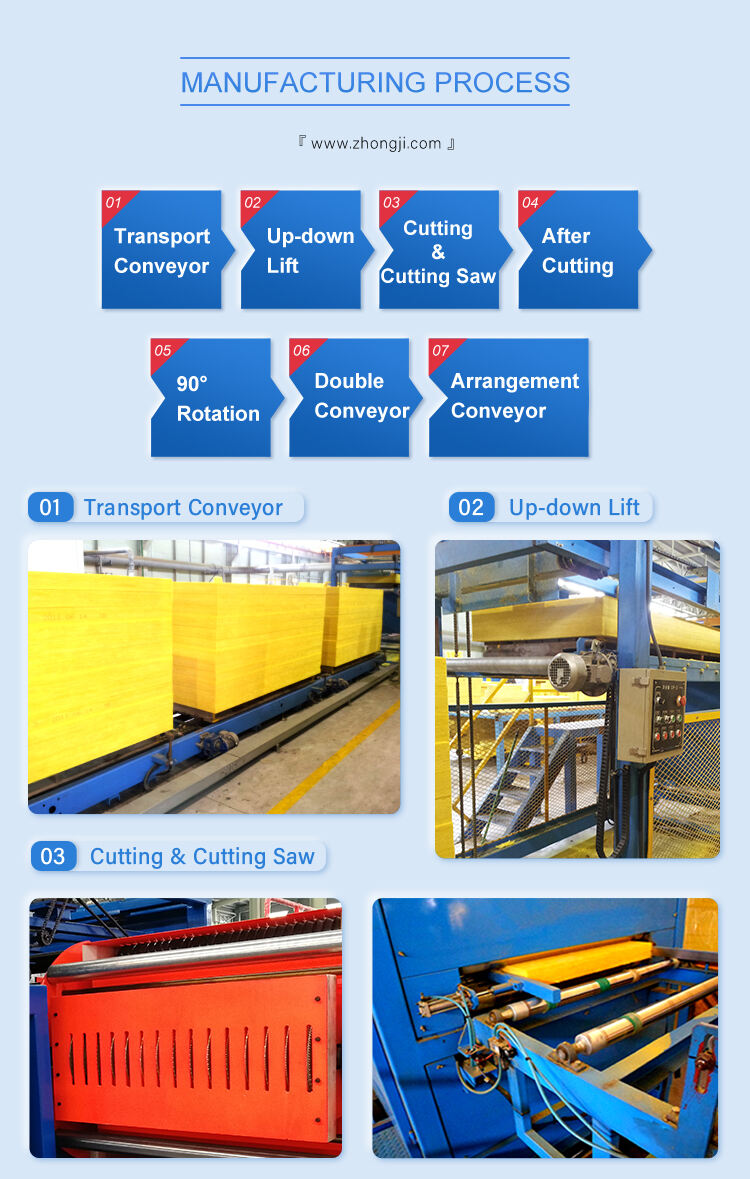
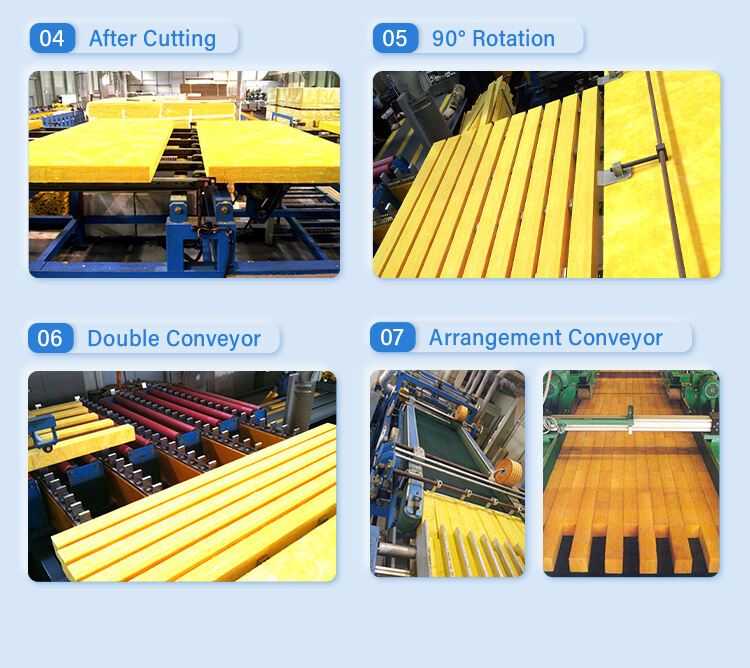
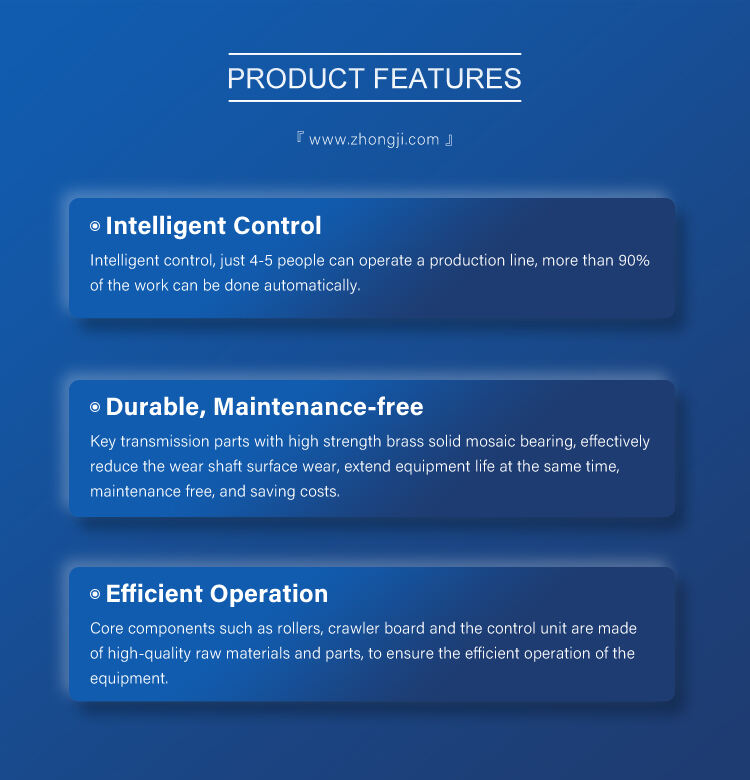
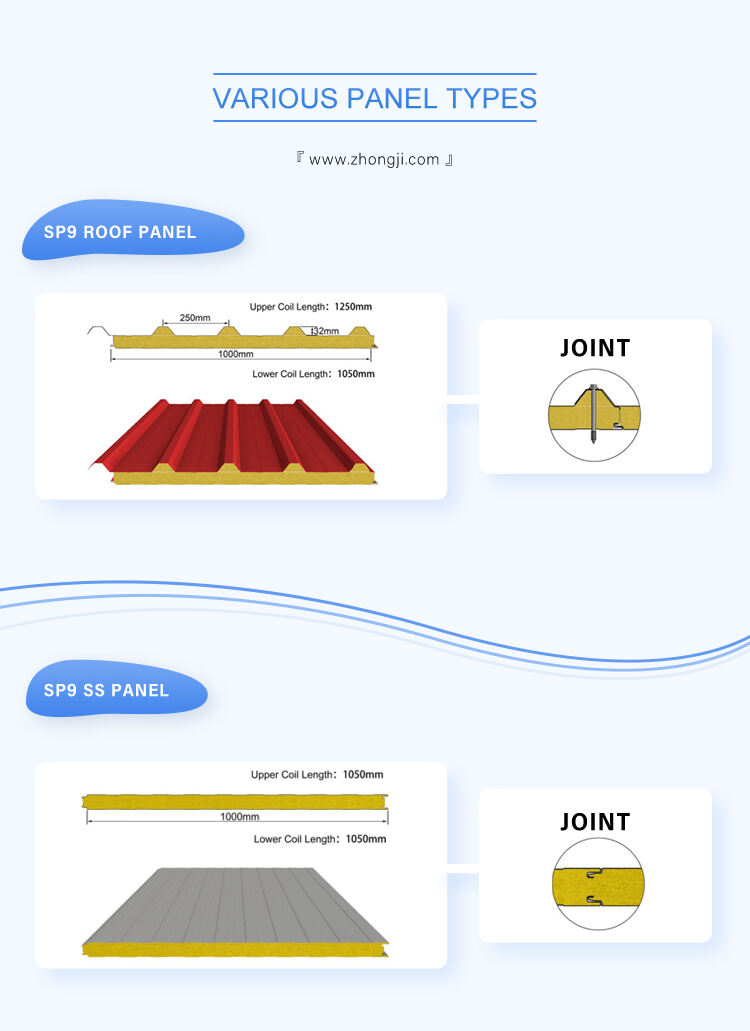
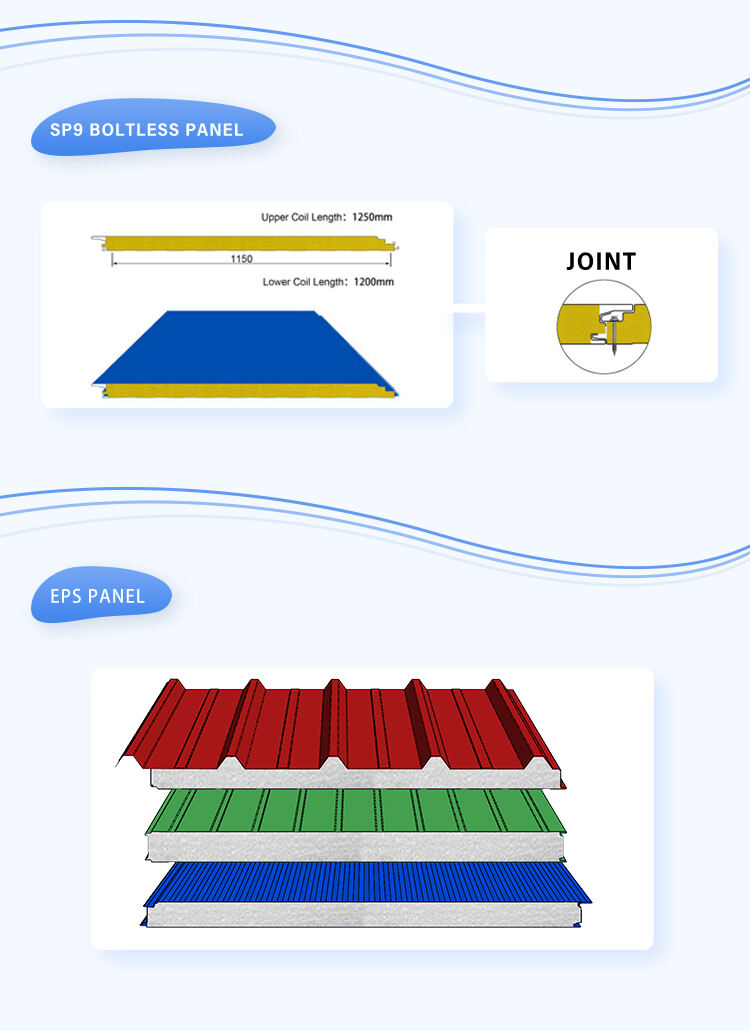
ITEMS
|
TYPE/UNIT
|
SP-PU-C
|
Production Line Speed
|
m/min
|
5~7
|
Total Power of Production Line
|
kw
|
31
|
Total Length of Production Line
|
m
|
42
|
Net Weight of Production Line
|
ton
|
30
|
Thickness of Finished Panel
|
mm
|
50-250
|
Color Steel Sandwich Panel Specifications
|
mm
|
Width: 1000 ~ 1200
Thickness: 0.2~ 0.8
|
3. The sandwich panel laminator uses rubber-coated roller type laminator to protect the color paint on the colored steel as well ascompleteduring the pressurizing of the sandwich panel.
4. The sandwich panel laminator has a high quality and thick wall rectangular steel welding method, which can get rid of the rust, polishing, smoothing and aging treament.
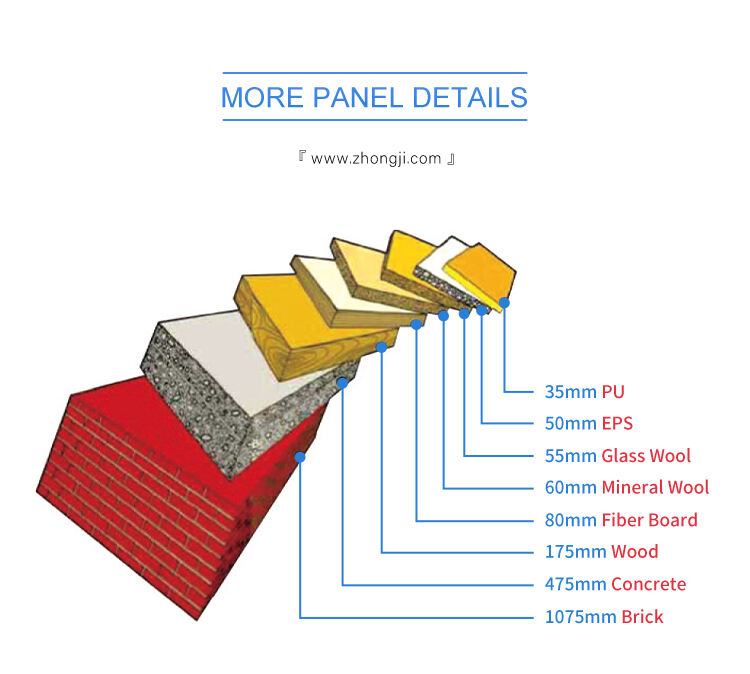
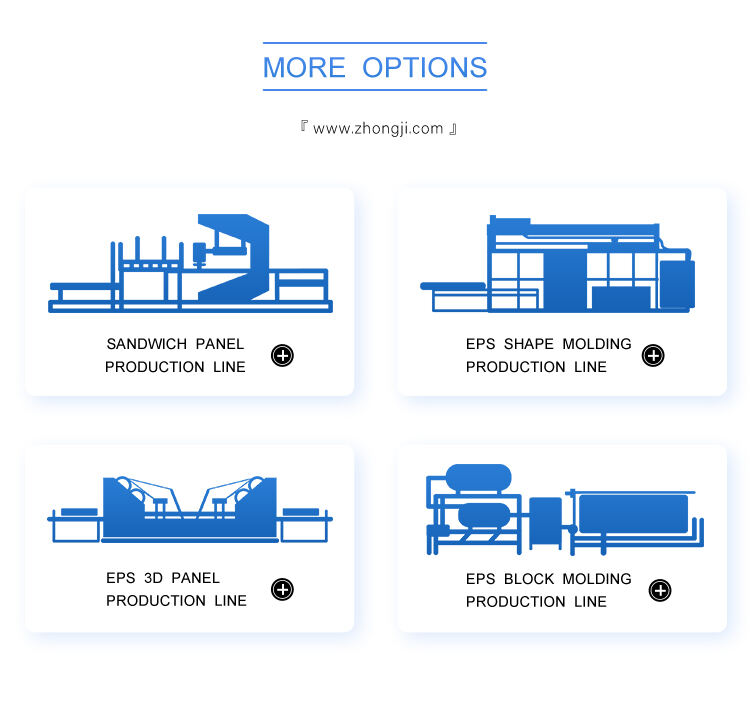
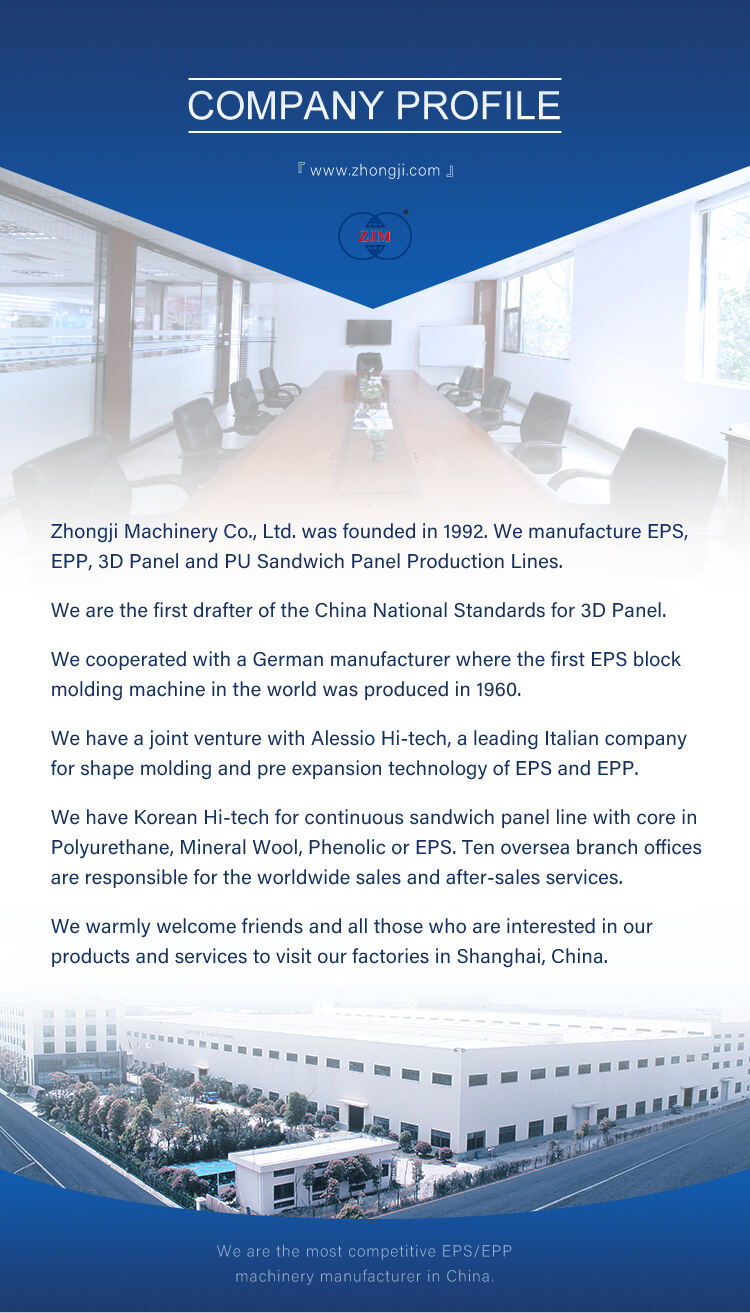
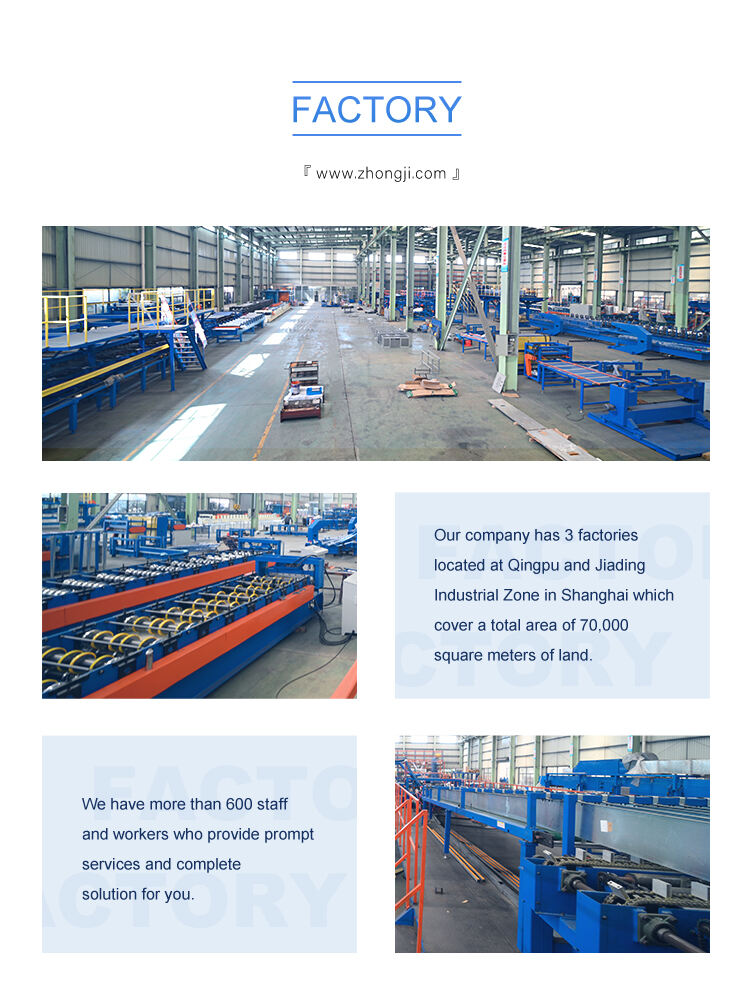
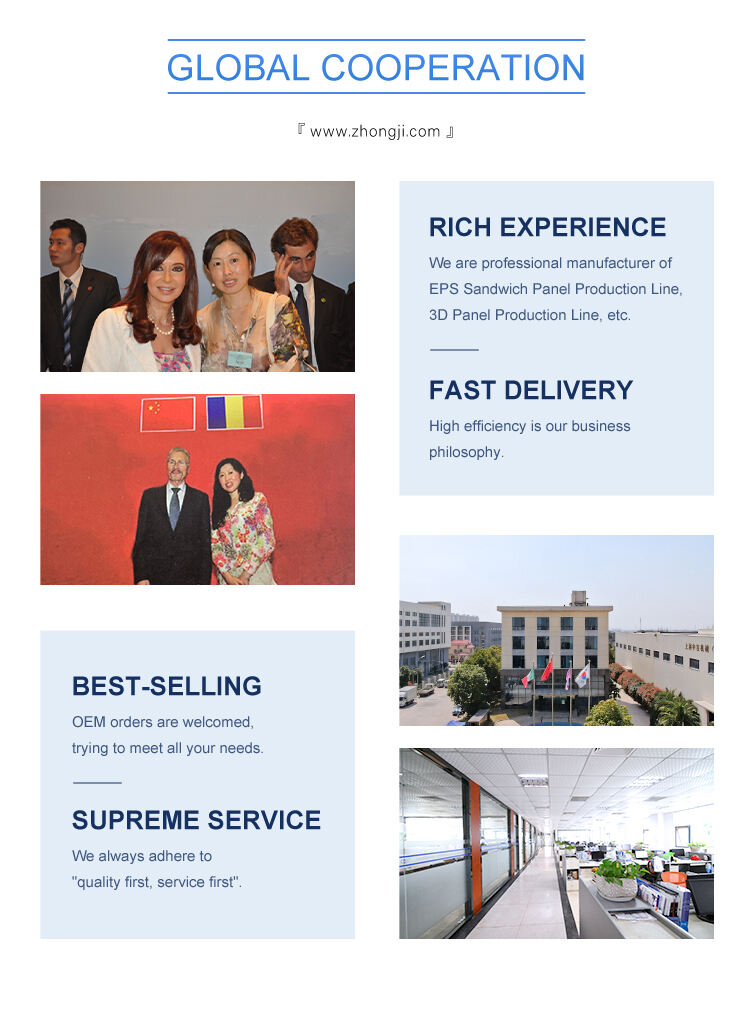
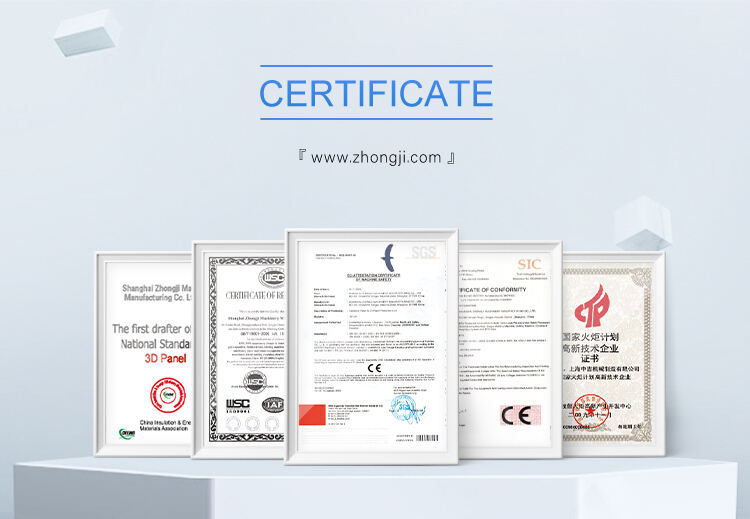
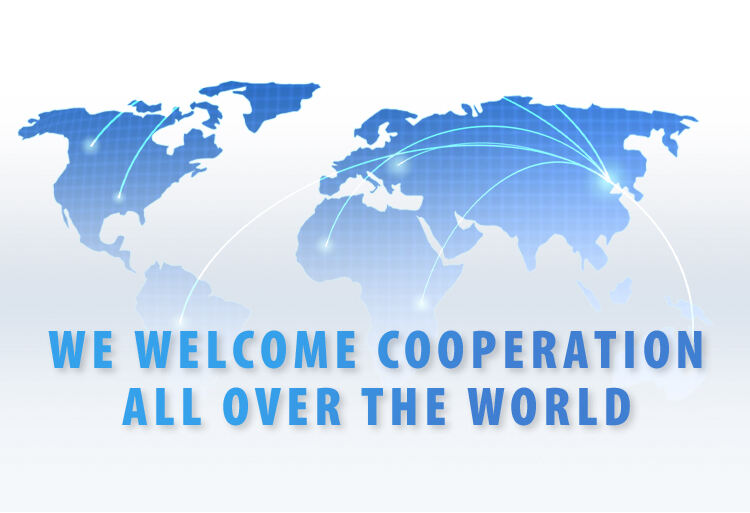
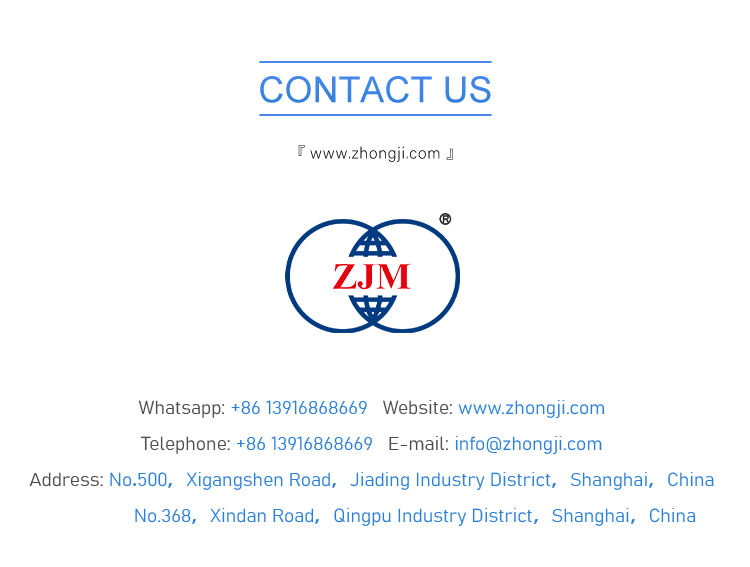
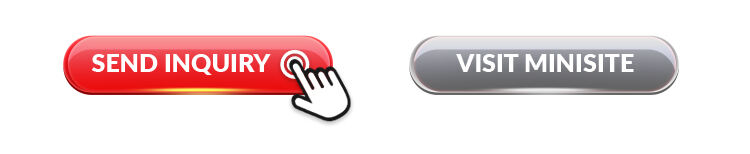